WS2 Applications | Application Areas | Cutting Tool Analysis | Material Properties
Bearing, gear & cutter life extended by 200 – 500%.
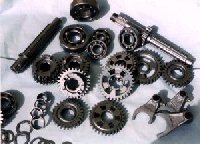
Application Areas Include:-
High Vacuum, High Temperature, Clean Room, Aerospace, Nuclear, Cryogenics, Machine Tools, Racing Engines, Cutting Tools, Die Casting
Benefits and Capabilities of WS2
- Solves problems such as: friction, excessive wear, seizing, galling and fretting.
- Withstands loads up to 350,000psi at temperatures between -273oC to 650oC.
- Enhances the performance of all oils and greases.
- Overcomes or reduces mechanical lubrication problems improving performance and extending service life up to
300-500%. - Eliminates and reduces costly maintenance problems that cause breakdowns and expensive downtime by stopping galling fretting and friction caused by dissimilar metals and their different hardnesses.
- Maintains the dimensional integrity of the substrate to within 0.5microns with no buildup.
- Is inert, inorganic, non-toxic, non-distortive, non-corrosive and resistant to most fuels and solvents.
- Resists carbon build-up from burnt deposits due to its extremely low coefficient of friction – less than half that of Moly and Teflon.
- Molecularly bonds to all materials and platings.
WS2 Applications

WS2 stops Pickup and Seizing on SS and Titanium
WS2 is finding many applications where the stopping of pickup or seizing is important. These screws are for a medical application which requires servicing every 3 to 5 years. Finding the parts seized is not an option.
Stainless steel parts within hydraulic systems and titanium parts for aircraft/space systems are typical application areas. Parts can be masked.

WS2 Extends Life of sliding parts
The cost of downtime due to wear of sliding parts can be dramatically reduced by specifying WS2 on sliding machine parts. The surface treatment is applied without heat and at 0.5micron thick does not affect engineering tolerances.
Use WS2 where conventional lubricants cannot be tolerated, where oils/grease are allowed their performance is enhanced.

WS2 Extends Gearbox Life
These gears are from a high-precision gearbox where WS2 is applied to reduce friction and extend life. Coated gears run with lower friction, higher efficiency (7-9%), will run at higher speeds and with a significantly longer life.
A Formula 3000 team owes its success to its WS2 coated gearbox. WS2 coated CV joints took part in the Paris – Dakar rally.
WS2 and Gearboxes:-
- The coating is 0.5 micro thick so no engineering changes are necessary will not chip or peel. No heat is used in its application. WS2 is used with usual gearbox oil.
- The coating is porous and has an affinity for oils to ensure you always have a lubricant film (oil and WS2) between bearing faces.
- WS2 is very low friction so less heat is generated within the gearbox. We are told by our US licensers that the US Army Airforce is considering using WS2 to extend gearbox life in the event of small arms damage to helicopter lubrication systems.
- WS2 will extend the life of your gearbox. You may be able to run with less oil onboard.
Gear shifting will require lower forces (Smaller Actuators?) and be smoother and faster in operation. - WS2 delays the onset of micropitting.

WS2 extends life of Ceramic Ball Races
A specialist bearing company routinely supplies ceramic ball bearings to its customers.
WS2 has been shown to extend the life of such bearings by enabling a “self healing” property of WS2 coated bearing to recover from shocks which would otherwise cause bearing failure.

WS2 Extends HSS Cutting Tool Life by 2 to 5 times
Tests have been done in the UK using WS2 as a coating on a HSS broaches. The life of the broach was extended by 5.5 times over an uncoated broach. A high speed tungsten carbide TicN coated milling cutter used for milling turbine blades was coated with WS2 – its life was extended by 2.0 times. A 2.8mm solid carbide drill coated with TiN cutting an aluminium alloy drilled 2200 holes – coating with WS2 extended the life to 7000 holes.
These cutters used normal cutting fluids during operation (after coating). In the US WS2 is used to extend the life on a range of cutting tools from gear hobs, broaches, taps, milling cutters & centre drills.
Benefits are:-
- Cutting edges remain sharp – we have coated razor blades for plastic film manufacture.
- The very low coefficient of friction reduces the heat generated in chip formation. Chips are well formed.
- WS2 prevents the build-up of material on the tooth face.
- WS2 is chemically inert so does not react with materials such as Titanium.
- WS2 withstands temperatures upto 650oC.
- Allows you to increase speeds and feeds and/or extends tool life.

WS2 is a lubricant in High Vacuum
A company with vacuum and compressor experience supply special purpose machinery for high vacuum research facilities in the UK and abroad. Previously they used MoS2 to lubricate bearings for use in such machines.
This was a time consuming and costly process. The company have now switched to using WS2 coated bearings which provides a quicker and lower cost solution to lubrication at high vacuum.
WS2 Lubricates at Cryogenic Temperatures
An Aerospace laboratory was trying to get a stepping motor to work at 4oK. We were asked to coat the bearings after which it worked quite happily.

WS2 Prevents Nut Seizure on Routing Head Spindles
The manufacturer of routing heads reported an occasional seizing of the collet tightening nut on to the head spindle.
After coating the threads with WS2 the problem did not re-occurr.
Zinc Diecasting
WS2 is also being used to stop galling and pickup in metal die casting. With coated ejector pins one company achieved 25,000 shots without any maintenance on the tool – a record for them!
Application Areas
Cutting Tools:
- End mills
- Roughing mills
- Jig reamers
- Broaches
- Centre Drills
- Drills and taps
Linear bearings used in:
- Waterjet cutting
- Milling
- Positioning devices
Ball & Roller Bearings:
- Vacuum and Laser applications
- Nuclear applications
- Clean rooms
- Medical devices
- Food processing
- Wet or caustic applications with polymer grease
Video Recorder:
- Hi speed duplication
Shafts:
- High speed spindles
- Cart wheels
- Packaging
- Aluminium rolling mills
Ball Screws:
- Thompson type shafts
- THK, IKO & NSK linear actuation and positioning devices
Automotive:
- All engine parts,
- Main bearings,
- Big End, Little End Bearings
- Gear Boxes
- Wheel bearings, CV joints
- Transmissions, Rear end differentials
Gears:
- Copying equipment, paper handling devices, printing presses
- High temperature open faced, non wet lube applications
- Clean rooms
High load heavy equipment for ease of disassembly Electric Motors:
- Including Generators,
- High speed and fractional hp
Shafts:
- Motor drives
- Internal/External splines shafts
- ACME Threads
- Dental motors, Medical Motors, Turbine Engines
- Wear plates, Gibs
Cold Forming:
- Canning machinery. Can be coated onto titanium nitride to reduce friction and wear.
- Tooling cold handling
- Crimping tools
- Forming tools
- Galling problems of Stainless on Stainless
- Galling problems of Aluminium on Aluminium
Conveyer systems, Glass plants, Paint spray systems Chains:
- Roller chain
- Link assemblies
- Glass plants
- Paper-mills
- Food processing
- Clean room applications
- Machine assembly sprocket grip chain
- Automotive conveyor
Valves:
- Servo valves,
- Solenoid,
- Needle,
- Metering valves,
- Ball valves,
- Fuel automotive injection systems,
- Diesel hydraulic valves and nuclear systems
Connectors:
- Stainless steel components,
- Hydraulic, fuel, air
- Applications where galling is a problem
Investment Casting Tooling:
- Eliminates the use of silicon sprays and extends life of moving parts
Plastic Injection Moulding & Extrusion:
- All mould components which contact resin
- Slides, gibs, Ejector Pins
- Inserts.
- Enhances flow 3-9% and increases productivity from 5-11% on average.
- Replaces release agents, does not transfer to finished parts.
- Can be coated on top of chrome plating and other hard coatings
Metal Die Casting:
- Useful lubricant between parts of multipart dies, to prevent seizing, where lubrication is difficult due to high temperatures. Release agent with Zinc
Welding/Cutting:
- Use on nozzles & machine guards where spatter needs to be easily removed
Cutting Tool Study
Investigation of tribological properties of hard coatings for cutting tools
• B.P. Bandyopadhyay, U. North Dakota, Grand Forks ND
• E. Fabiszak, Micro Surface Corp, Morris IL
• GR Fenske & FA Nichols, Materials & Components Technical Division
• Argonne National Laboratory, Argonne IL
ABSTRACT
Manufacturing firms are constantly striving to improve product quality and productivity while reducing costs. proper selection of cutting-tool materials can greatly improve the productivity and quality of metal products. Hard wear-resistant coatings such as titanium carbide( TiC) and titanium nitride (TiN) applied to carbide and high-speed-steel (HSS) tool inserts are widely used in the metal-cutting industry. Recent studies have shown that premature failure of these coatings at high metal-removal rates is due to softening of the substrate.
It is believed that coating lifetime could be increased significantly by reducing the frictional heating in the tool insert. This has led to the concept of applying a thin layer of tungsten disulphide (WS2) as solid lubricant on top of TiN-coated inserts to reduce frictional heating and increase tool life. A systematic study was conducted to evaluate the performance of tool inserts with different wear-resistant coatings. Approximately 100 each of HSS and carbide tool inserts that were (1) uncoated, (2) coated with WS2 only, (3)coated with TiN only, and (4)coated with TiN and then with WS2.
The experiments were done on a numerically controlled lathe capable of continuously varying the spindle speed. During the turning operations , the three components of cutting force were monitored with a strain gauge dynamometer. Flank, notch, and crater wear were measured ate regular intervals by an optical microscope. Prior to the experiment, each coated insert was examined optically to ensure proper coatings had been applied to the rake and flank surfaces.
No cutting fluid was used in the experiments. Inserts coated in WS2 were found to have significantly lower flank wear than other inserts than inserts not coated with WS2. Application of WS2 reduced the flank notch wear of uncoated and TiN-coated inserts, with the largest reductions being observed for inserts coated with TiN and WS2. However, if tool life is defined as cutting time until the insert failed catastrophically, then TiN-coated inserts (no WS2) had the best lifetime performance. Details of the results are presented in the paper.
This paper was presented at the Japan International Tribology Conference Nagoya, Japan, October 29-November 1, 1990

Material Properties
Composition – Modified Tungsten Disulphide (WS2 ) in laminar form.
Coefficient of Friction – 0.030 dynamic, 0.070 static. ( WS2 on WS2 )
Load Capacity – Same as substrate up to 350,000 psi
Adhesion – Molecular bond, no cure time, applied at ambient temperature
Temperature Range – Lubricates from -460oF to 1200oF ( -273oC to 650oC) in normal atmosphere, -350oF to 2400oF (-188oC to 1316oC) at 10-14 Torr
Chemical Stability – Inert, non-toxic, corrosion resistance. Non magnetic
Substrates – All ferrous and non ferrous metals, man-made solids /plastics
As A Substrate – Accepts most paints, all platings, is compatible with solvents, fuels and oils
LOX Compatibility – Insensitive to detonation by or in presence of oxygen
Hardness – approximately 30 Rockwell C
Thickness – 0.5 microns (0.000020 in)
Military Specification – Processed to DOD – L – 85645
