Cores & Cavities | Aluminium Moulds | Closure Applications | Prevent Pickup | Enhancing Flow | Blow Moulding Applications
Very Low Friction Dry Lubricant
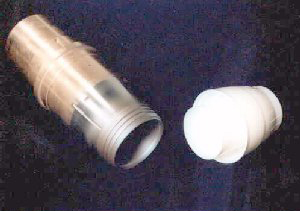
Stop Wasting Time and Money On:-
- Sticking Cores
- Moulds not filling properly
- Parts sticking in the mould
- Pickup on moving mould parts
- Lubricant Contamination
- Streaking & Drag Marks
Major Benefits of WS2 for the Plastics Industry:-
- Increases productivity – more parts per hour – parts not sticking in the mould.
- Enhances the flow of resin in moulds due to its low coefficient of friction.
- Parts release quicker.
- Allows the reduction in moulding pressure and temperature.
- Reduction in part weight as resin is not packed as tight.
- Eliminates streaking and drag marks, moulds fill more easily reducing rejects.
- Eliminates use of other release agents. Eases colour changes and cleaning operations.
- Not transferred to finished parts so no washing required prior to printing.
- Can be applied to metal-on-metal die parts and moulding machines as a long lasting, heat proof, to reduce wear and seizing.
- Application to No.1 diamond finish . . . lens quality.
- Can be applied into slots and holes as small as 0.060″
- May be applied over the whole mould or in specific inserts, cavities or on core pins.
- Bonds to all metal or plastic materials and platings and cannot be removed without removing the substrate.
- Maintains dimensional integrity of mould to within 0.5microns cannot be build up to greater .
- Eliminate problems in commissioning new die sets.
- Resists carbon build-up from burnt deposits due to extremely low coefficient of friction.

General Notes:-
- WS2 is a surface treatment not a spray.
- WS2 is applied at ambient temperature.
- WS2 cannot peel or chip.
- WS2 is suitable for medical/clean room moulding.
- WS2 is 0.00002in thick so needs no special engineering.
- The parts have to come to us for treating.
- We can handle parts up to 5 tonne in weight (1200mm x 2200mm).
- Most parts can be processed with one working day of receipt.
- We offer a while you wait coating service.
Aides Release on Cores & Cavities
Here are a few of our successes to give you some idea of what problems other people are using WS2 to solve:-

WS2 aids release in big moulds
The mould for a large tote bin had caused problems over a long period. The company had tried roughening the edges in an attempt to improve release but without success.
We coated the mould. Thereafter release improved significantly. The mould core shown here weighed in at 1.5 tonnes.

WS2 Solves release for Cosmetics Packaging (with 5p piece)
This is a small thin walled part with 0.25mm internal webs. Parts would occasionally stick in the cavity. The sticking got a whole lot worst when regrind was used. Since the mould had quite thick sprues a lot of material was not reusable.
We coated the cavity inserts of the mould. The cycle time was able to be reduced from 8 sec to 7 seconds and sticking was eliminated.
The first shift after coating the mould the production increased from 22k to 32k on 100% regrind. On going improvement 18k/day. – solved with WS2 Coating.

WS2 Solves release for Deodorant Packaging
The cavities of a major deodorant client had a rather special moulding made from a clear PET material which kept sticking to the mould cavity.
A small modification to the gate area plus coating with WS2 solved the problem. As a bi-product of coating the cavity the filling time was reduced by 0.9 seconds.
Also the polished cores were causing drag marks on the finished part. These were coated…. no more drag marks. Side-actions have been coated to help filling and surface finish.

WS2 releases Recessed Nameplates
Moulding were sticking in these recessed nameplate blocks.
Also the stainless steel from which they were made was picking up due to their sliding action. Both problems solved with WS2.
Sealant Packaging
The company moulds sealant packaging cartridges 44mm dia x 220 long which were regularly sticking on the cores.
WS2 coated cores ran without problem. The company sends mould cores & cavities for coating with WS2 on a regular basis.
Bearings Moulder
One part in Acetal stuck in the mould about once per shift, after coating the part ran for a 4 day test period without sticking once.
Since then various moulds have been coated on a regular basis.
Medical Moulder, South Coast
Small finger cores 4mm x 1mm x 15mm long were sticking. These cores required high polish and then they had to be “run-in” for 24hrs before the production was usable.
We coated the polished cores which proved usable immediately.
We then coated unpolished (sparked) cores these also were usable without the “running-in” period. A very happy man.
Trade Moulder
Having severe difficulty moulding a castelated core. WS2 coated core “while you wait” while worked immediately on retrial.
WS2 Aides Release on Aluminium Moulds
Here are a few of our successes to give you some idea of what problems other people are using WS2 to solve:-

Midland Moulder
Aluminium box mould 120mm x 120mm x50mm deep with severe release problems. The company had tried polishing to no avail.
We coated the cavity with WS2 the next morning parts were delivered to the customer. The larger computer panel mould pictured here was also coated to help release.

East Midlands Moulder
Aluminium drinks tray core about 300mm. dia. with severe release problems. The company had tried polishing to no avail.
The project had been abandoned. We coated the core with WS2. At the next trial trays were coming off perfectly. More problem moulds sent for coating.
In Closure Applications
WS2 affords significant benefits when used in closure applications.
These are:-
- The mould will fill faster.
- You can start unscrewing before you otherwise could with uncoated cores.
- The cycle time will be reduced.
- Considerably less torque will be required during unscrewing.
- Higher quality with reduction in scrap parts. Reduction in down time.
Here are a few of our successes to give you some idea of what problems other people are using WS2 to solve:-

Lever Brothers – Comfort Bottle Closure
The company concerned has a number of 6 year old 12 impression unscrewing tools. The tools were beginning to show their age and working had become problematic.
WS2 coated the central steel cores and the berylium copper unscrewing sleeves and returned these parts the same day. The tool went back into service and is working perfectly. Other tools from the same suite have been sent for coating.
Hilton Hotels – Shampoo Bottle Closure
This tool would not work! WS2 coated the unscrewing cores and the central bronze cores.
The tool went back into service with a much reduced cycle time and required less torque to unscrew. Other tools are being sent for coating.
Oil of Ulay – Closure
After coating of the unscrewing cores with WS2 the cycles time went from 21 seconds down to 17 seconds.

WS2 Helps South West Toolmaker
A major customer with experience of WS2 in the United States elects to have all new unscrewing tools coated to help their release.

Northern Precision Moulder
Moulding bump off closure type fitting WS2 prevented distortion. Problem with crushing on moulding during “bump-off” solved with WS2.

Closure Moulder A
Moulding bump off closure type fitting WS2 prevented distortion.
Problem with crushing on moulding during “bump-off” solved with WS2.

Closure Moulder B
Has had a number of tools coated with Ws2 and keeps coming back.

SouthWest Toolmaker
This toolmaker was sceptical about WS2 ability to stop pickup on stainless steel mould parts.
Since his first use he continues to send tools on a regular basis.
Prevents Pickup on Stainless Steel Mould Parts
Here are a few of our successes to give you some idea of what problems other people are using WS2 to solve:-
Major Producer of Cable Ties – Ejector Pins
This moulder had used WS2 successfully on the tie lock inserts which had the effect of removing tool room personell from the production department and reducing downtime.
Some time ago he had some ejector pins coated which he assembled with a little grease. Thirty months later (after cycling the whole time at 7 seconds) the mould was inspected…there was no wear on either holes or the pins! He now coats all ejector pins!
Medical Moulder uses Coated Ejector Pins
A medical moulder had used WS2 coated ejector pins without grease and got over 2 million cycles without the mould requiring servicing! This was significantly better than other moulds in the set that had not used WS2.
Major Cosmetic Clean Room Moulder
From experience of WS2 dry lubrication gained in the USA this moulder has made the decision to coat all wearing parts of all moulds.
Mike – Southern Precision Engineers
Mike has tried WS2 on a number of tools to prevent pickup. Tools were for a major drugs delivery company.
Peter – Trader Moulder
Peter has also tried WS2 on a number of tools to prevent pickup.
DMS – Die Mould Services – Tel. 01494 523811
You can order WS2 coated ejector pins direct from Die Mould Services Co. Ltd.
Enhances Resin Flow 3-9%
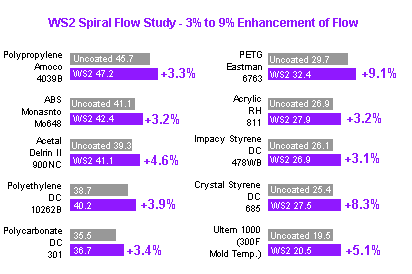
Here are a few of our successes to give you some idea of what problems other people are using WS2 to solve:-
Plastic Bearings Moulder
Part with very thin web (less than 1mm thick) – mould not filling properly – solved with flow enhancing WS2 Coating.
WS2 Helps Flow in Deodorant Packaging
The cavities of a major deodorant client had a rather special moulding made from a clear PET material which kept sticking to the mould cavity. A small modification to the gate area plus coating with WS2 solved the problem.
As a bi-product of coating the cavity the filling time was reduced by 0.9 seconds. Also the polished cores were causing drag marks on the finished part. These were coated…. no more drag marks.
Side-actions have been coated to help filling and improve surface finish by removing sink marks.
WS2 Helps Flow in Floor Tiles Mould
A major floor tile moulder moulder was having problems with slip-stick flow marks on the surface of the finished product. We coated the mould plates – no more marks – a happy man!
WS2 – Spiral Flow Study
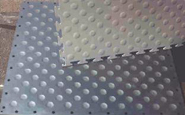
The Spiral Flow Study and Analysis was conducted by Western Washington University totally independently and in strict compliance with SPE procedures. All test resins were run to their manufacturer’s specifications.
The study was conducted to quantify flow enhancement afforded by WS2 coating when applied to injection, blow and extrusion tooling.
Over the course of four years virtually all WS2 customers experienced improved product quality due to reduced required operating pressure and temperatures, as well as significantly lower operating costs resulting from faster cycling and increased tool life.
The following test data includes the most often run resins and illustrates the flow enhancement provided by WS2. The standard MUDD spiral tool was used for the study.
— MATERIAL — | -Uncoated- | -WS2 Coated- | % Improvement |
Polypropylene – Amoco 40398 | 45.7 | 47.2 | +3.3% |
ABS Monsanto Mo648 | 41.1 | 42.4 | +3.2% |
Acetal – Dalrin II 900NC | 39.3 | 41.1 | +4.6% |
Polyethylene DC10262B | 38.7 | 40.2 | +3.9% |
Polycaronate DC301 | 35.5 | 36.7 | +3.4% |
PETG Eastman 6763 | 29.7 | 32.4 | +9.1% |
Acrylic RH811 | 26.9 | 27.9 | +3.2% |
Impacy Styrene DC478WB | 26.1 | 26.9 | +3.1% |
Cristal Styrene DC685 | 25.4 | 27.5 | +8.3% |
Ultem 1000(300F Mould Temp) | 19.5 | 20.5 | +5.1% |
Quality Improvement in Blow Moulding
Here are a few of our successes to give you some idea of what problems other people are using WS2 to solve:-
Bottles Blow Moulde
This moulder was suffering from having to shut bottle lines down due to burnt-on carbon and plastic on head tooling causing streaking and drag marks on the finished product. The lines were shut down for head cleaning about once per week. The build up of carbon was aggravated by not turning down the head temperatures when the line was stopped for other reasons.
CMB have found that WS2 coated head tooling required the line to be stopped for head cleaning only after about 8 weeks. Prior to this each time the line was stopped the carbon just came off the heads on the first one or two bottles after restarting. Machine settings could be maintained on an ongoing basis. WS2 increased product quality, reduced streaking and drag, and increased productivity.
Dale Maddox – Johnson Controls, Manchester Michigan
“We have tried a whole bunch of mould coatings, probably 15 in all, WS2 is the best of the lot! It makes the filling of deep moulds easier and eliminates streaking and drag marks. Can be coated on top of chrome and other hard coatings.”
Mr. Frank Rukavina, K&M Plastics, Elk Grove Village, Illinois
“WS2 increased product quality, reduced streaking and drag, Machine settings maintained on a constant basis”